Precision Milling---Diamond coated tools for graphite milling
Diamond coated tools is IDI’s first product line from the beginning of the company. The complexity of manufacturing diamond coated tools provided us very good experience in carbide material, tool grinding, coating and quality control techniques. Over the past 20 years, IDI has continuously improved our diamond tools by trying new materials, grinding methods, coating solutions and even tool cleaning procedures. New quality control instruments and techniques have been implemented to ensure tool quality and performance.
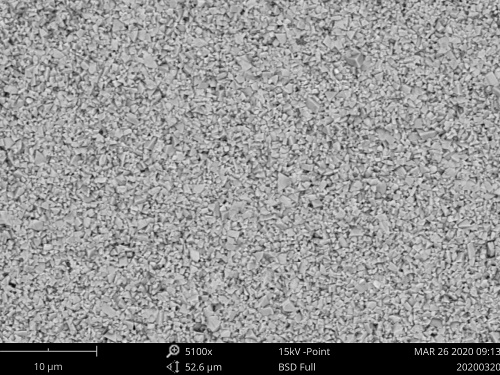
Substrate from the beginning
Our material: D17, made in Europe, is our sixth-generation carbide material specially designed for diamond coating. Coarse grain size, low cobalt content and special additives provide highest diamond film adhesion. D17 material is used in all our diamond coated tools for both metric and imperial series. All carbide rods(tool shank) are ground within h5 tolerance.
Diamond coating
DG diamond coating, done in Europe, is the result of close cooperation of material, grinding, polishing, post and pre-treatment, coating, inspection and cutting test teams. It is a multilayer diamond film coated on our D17 substrate. With several layers of nano and micro crystalline diamond films overlapped each other, this coating solution provides not only the highest hardness of diamond but also smooth lubrication during graphite milling. Thanks to the fine-tuned coating process, our diamond film is now among the very best and most reliable diamond coating in the industry.
Tool grinding---temperature and internal stress
All IDI graphite tools are ground by direct-motor- drive grinding machines with granite structures which ensures zero back lash and high damping ratio. Not like big tool grinding shops who put all machines in one facility, IDI put every two grinding machines in one cell where temperature is tightly controlled within ±1oC and coolant is controlled within ± 0.1oC. Every tool edge grinding is composed of both roughing and finishing steps that make sure there is no internal stress within the carbide so that the tool won’t bend after high temperature coating process.
Tool monitoring and tracing---every details
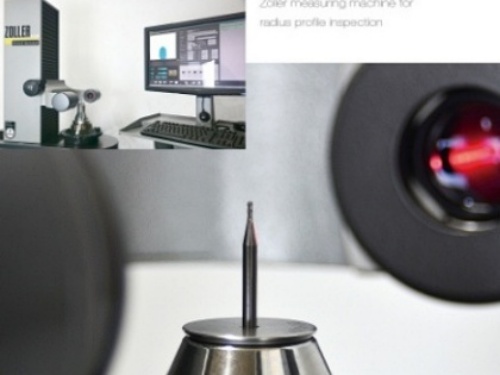
Having an excellent facility and grinding machine is not enough. Carbide material and tool geometry must be monitored during every process. From carbide laser mark for material tracking to run out and diameter checked, every detail is monitored during the whole process. All tools will be inspected and measured after coating before putting on the shelf.
Today IDI is one of the few tool makers in the world that offers a complete product range of diamond tools with top precision and reliability. We provide both metric and imperial unit lines ranging from 0.2mm to 12mm and 0.01” to 1/2” respectively. You can always find what you need for your graphite milling process.